Shooting gunite is a critical step in the construction of a gunite pool. Gunite is a mixture of cement, sand, and water that is shot onto a rebar framework to create the pool’s structure. Understanding the timeline for shooting gunite is important for both homeowners and pool contractors to ensure a smooth and efficient construction process.
In this article, we will discuss the various considerations and steps involved in shooting gunite, including site preparation, rebar placement, and the gunite application process. We will also explore the factors that can affect the shooting time, as well as safety precautions and potential challenges that may arise during the process. Additionally, we will discuss the impact of weather conditions on gunite shooting and strategies for working around weather constraints.
By understanding the timeline and considerations involved in shooting gunite, homeowners can have a clear picture of the construction process and better plan for the completion of their gunite pool. This knowledge will also enable them to effectively communicate with the pool contractor and ensure a high-quality and timely construction project.
Table of Contents
Key Takeaways
- Shooting gunite is a crucial step in building a gunite pool, involving the application of a mixture of cement, sand, and water onto a rebar framework.
- Pre-shot considerations play a vital role and involve site preparation (clearing, excavation, and form setup) and preparing the rebar (proper placement and reinforcement).
- The time required for gunite shooting can vary depending on pool size, complexity, crew experience, and weather conditions.
- Gunite shooting requires specialized equipment, including a gunite machine, nozzle, air compressor, and hoses.
- The gunite application process involves mixing the gunite, selecting the application method (dry or wet mix), and using skilled nozzle operators to ensure consistent thickness and reinforcement.
- The estimated time for gunite shooting in an average-sized residential pool is 1 to 3 days.
- Factors affecting shooting time include pool size, complexity, crew skill, and weather conditions.
- Efficient gunite shooting tips include proper planning, consistent workflow, optimal mix ratios, minimizing downtime, proper nozzle techniques, crew size optimization, equipment maintenance, continuous training, and adherence to safety protocols.
- Safety precautions are essential during gunite shooting, including the use of personal protective equipment, proper training, maintaining a safe working environment, equipment safety, communication, emergency preparedness, and adherence to OSHA guidelines.
- Weather considerations are crucial, and gunite shooting is best carried out in dry, mild, and low-humidity conditions. Extreme temperatures and precipitation can pose challenges, and temporary measures may be necessary to work around adverse weather conditions.
Pre-Shot Considerations
Pre-shot considerations play a crucial role in ensuring that the gunite shooting process goes smoothly and efficiently. These considerations involve site preparation and preparing the rebar, which are important steps that need to be completed before shooting gunite. Let’s take a closer look at each of these pre-shot considerations.
Site Preparation
Before the gunite can be shot, the construction site needs to be properly prepared. This involves clearing the area, excavating the ground, and setting up the forms.
- Clearing the area: The first step in site preparation is clearing the area where the pool will be constructed. This includes removing any obstacles, such as trees, bushes, rocks, or existing structures, that would hinder the construction process. Clearing the area thoroughly will ensure a clean and open space for the pool construction.
- Excavation: After the area is cleared, excavation is done to create the pit for the pool. The excavation process involves digging out the ground to the desired depth and shape of the pool. This may require heavy machinery and professional excavation services to ensure accuracy and efficiency.
- Setting up the forms: Once the excavation is complete, forms need to be set up to outline the shape and dimensions of the pool. Forms are typically made of wood or metal and are used to create the mold for the gunite. The forms need to be sturdy and properly aligned to ensure the pool structure is uniform and consistent.
Preparing the Rebar
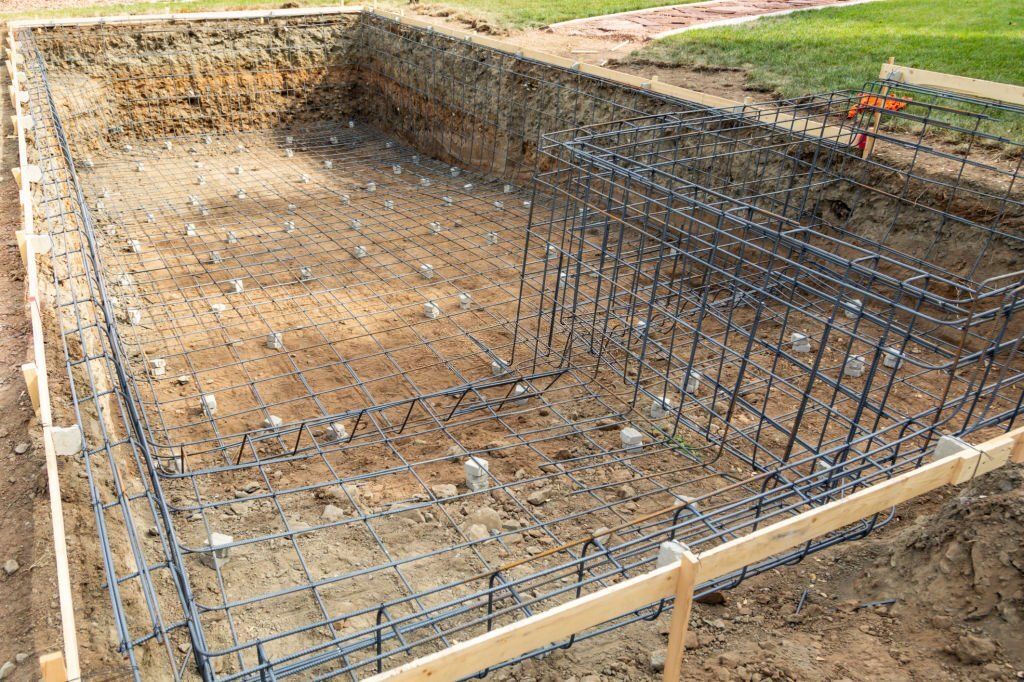
Rebar, short for reinforcing bar, is a critical component in constructing a gunite pool. It provides strength and structural integrity to the pool, ensuring its durability and longevity. Proper placement and spacing of the rebar are essential for a successful gunite shooting process.
- Proper placement and spacing: The rebar needs to be placed in a specific pattern and spaced evenly throughout the pool structure. The exact placement and spacing will depend on the design and size of the pool, as well as the engineer’s specifications. It is important to follow these guidelines to ensure proper reinforcement and adherence to building codes and regulations.
- Reinforcing the structure: Once the rebar is in place, it needs to be securely tied together to reinforce the pool’s structure. This is often done using wire or zip ties. The rebar needs to be tied tightly to prevent movement during the gunite application process. It is important to ensure that the rebar is completely covered by the gunite mixture to protect it from corrosion.
By properly preparing the site and rebar, pool contractors can set the stage for a successful gunite shooting process. These pre-shot considerations are essential in creating a strong and durable pool structure. Failing to complete these steps properly can lead to various issues, such as uneven pool surfaces, structural instability, and potential damage to the rebar.
Additionally, homeowners should also ensure that the pool contractor they hire has experience and expertise in site preparation and rebar placement. This will help to ensure that these important pre-shot considerations are done correctly, laying a solid foundation for the gunite pool construction.
It is also worth mentioning that the time required for site preparation and rebar placement can vary depending on the size and complexity of the pool design, as well as the efficiency and experience of the construction crew.
Therefore, it is important for homeowners to have realistic expectations regarding the timeline for these pre-shot considerations. Effective communication and coordination with the pool contractor will help homeowners stay informed about the progress and ensure that the necessary pre-shot considerations are completed in a timely manner.
Shooting Gunite
Shooting gunite is a critical step in the construction of a gunite pool. Gunite is a mixture of cement, sand, and water that is pneumatically applied to create a solid and durable pool structure. The gunite is typically shot onto a framework of rebar, which provides reinforcement and structural integrity to the pool.
Understanding the process of shooting gunite, the equipment required, and the factors that can affect the shooting time is important for both homeowners and pool contractors.
The Equipment Needed to Shoot Gunite
Before delving into the process of shooting gunite, it is important to understand the equipment required for this task. The key equipment for shooting gunite includes:
- Gunite machine: A gunite machine, also known as a dry-mix or wet-mix shotcrete machine, is used to pneumatically apply the gunite mixture onto the rebar framework. The machine typically consists of a hopper for holding the gunite mixture, a compressor for shooting the mixture, and a nozzle for directing the flow of gunite.
- Nozzle: The nozzle is an essential component of the gunite machine that is responsible for directing the flow of gunite onto the pool structure. It is operated by a skilled nozzleman who controls the angle, velocity, and density of the gunite stream.
- Air compressor: An air compressor is used to generate the necessary air pressure for shooting the gunite mixture onto the pool structure. The compressor supplies a steady flow of compressed air to the gunite machine, allowing for efficient and continuous application of gunite.
- Hoses: Hoses are used to transport the gunite mixture from the hopper to the nozzle. These hoses need to be flexible and durable to withstand the high pressure and abrasive nature of the gunite mixture.
Gunite Shooting Process
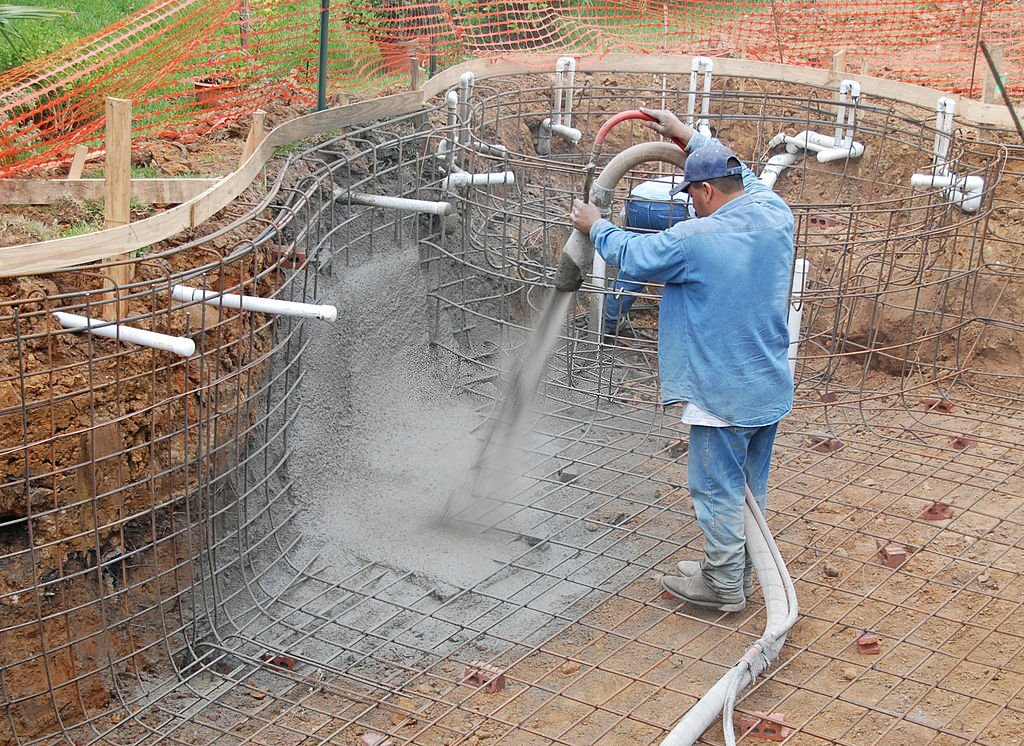
The gunite shooting process is a critical step in building a gunite pool. It involves the application of a mixture of cement, sand, and water, known as gunite, onto a framework of rebar to create the pool’s structure. This process requires skill, precision, and attention to detail to ensure a durable and long-lasting pool. Let’s take a closer look at the gunite shooting process.
Mixture Preparation
The first step in the gunite shooting process is the preparation of the gunite mixture. The mixture is typically prepared by combining cement and sand in the correct proportions. Water is then added to the mixture to create a workable consistency. The exact mix ratio may vary depending on factors such as pool design, local building codes, and engineer specifications. It is important to follow the recommended mix ratio to achieve the desired strength and durability of the pool structure.
There are two primary methods of applying gunite: dry mix and wet mix.
- Dry mix gunite: With the dry mix method, the dry gunite mixture is placed in the hopper of the gunite machine. Compressed air is then used to push the mixture through the hoses and nozzle, where water is added just before it is sprayed onto the pool structure. This method provides more control over the water content, allowing for adjustments to achieve the desired consistency.
- Wet mix gunite: In the wet mix method, the gunite mixture is pre-mixed with water before being placed in the hopper. The pre-mixed wet gunite is then sprayed onto the pool structure using compressed air from the gunite machine. The wet mix method is often preferred for its ease of use and efficiency.
Both methods can produce durable and high-quality pool structures when executed correctly. The choice of method may depend on factors such as crew preference, job site conditions, and specific project requirements.
Application Process
Once the gunite mixture is prepared, the gunite application process begins. This involves using a gunite machine to pneumatically apply the mixture onto the pool’s rebar framework. The gunite machine consists of a hopper for holding the mixture, an air compressor to generate the necessary air pressure, hoses to transport the mixture, and a nozzle to direct the flow of gunite.
The nozzleman, a highly skilled and experienced operator, controls the nozzle and guides the application of the gunite mixture. The nozzle is moved methodically and evenly across the pool area, ensuring complete coverage and consistent thickness. The nozzleman is responsible for adjusting the angle, velocity, and density of the gunite stream to achieve the desired results.
During the application process, the crew members work together to ensure smooth operations. They collaborate with the nozzleman, providing support, monitoring the mixture supply, and assisting in maintaining a continuous flow of gunite. Constant communication and coordination between the crew members are vital for effective and efficient gunite application.
Consistent Thickness and Reinforcement
One of the key objectives during the gunite shooting process is achieving consistent thickness and proper reinforcement of the pool structure. The crew needs to ensure that the gunite mixture is applied evenly across the entire surface of the pool, including walls, floors, and any other designated areas. The thickness of the gunite layer is critical for structural stability and longevity. It is essential to avoid any areas of excessive thickness or thin spots, as they can lead to structural weaknesses.
Proper reinforcement is another important aspect of the gunite shooting process. The rebar framework provides strength and support to the pool structure. It is crucial to ensure that the gunite fully encapsulates the rebar, providing a secure bond for structural integrity. The crew should verify that the spacing and placement of the rebar comply with engineering and design specifications.
Throughout the gunite shooting process, the crew must monitor the consistency of the mixture, adjust the application technique as necessary, and maintain focus on achieving consistent thickness and proper reinforcement.
How Long Does It Take To Shoot Gunite
Step | Description | Time Required |
---|---|---|
Surface preparation | Cleaning the surface, repairing damages, and applying a bonding agent or primer | Varies |
Equipment setup | Setting up the gunite equipment, including the spraying nozzle and hoses, compressor, and other tools | Few hours |
Mixing the gunite | Thoroughly mixing the gunite mixture to achieve the desired consistency | 1-2 hours |
Applying gunite layers | Applying successive layers of gunite to the surface | 1-2 days |
Shaping and finishing | Shaping and finishing the surface to achieve the desired texture and appearance | Varies |
The average time for shooting gunite in a swimming pool can vary depending on the size and complexity of the pool, as well as other factors such as crew experience and weather conditions. However, as a rough estimate, it can typically take anywhere from 1 to 3 days for the gunite application process for an average-sized residential swimming pool.
For small to medium-sized residential pools, the shooting time may range from 1 to 2 days. This includes the time for surface preparation, mixing and loading the gunite mixture, and the actual spraying of the gunite onto the pool shell.
For larger, more complex residential pools or commercial swimming pools, the shooting time may extend up to 3 days or more. This is because larger pools require more surface area to cover, and there may be additional features such as complex shapes, attached spas, or waterfalls that require extra time and attention during the gunite application process.
To get an accurate estimate of the shooting time for a specific swimming pool project, it is best to consult with a gunite contractor or construction professional who can assess the project’s unique parameters and provide a more precise timeline.
Factors affecting shooting time
The time required to shoot gunite can vary depending on several factors, such as the size and complexity of the pool, the experience and skill of the crew, and the weather conditions. In order to get an accurate estimate of the shooting time for gunite, it is best to consult with a professional pool contractor. They can assess the specific project details, such as the size and complexity of the pool, and provide a more accurate timeline based on their experience and expertise.
- Pool Size and Complexity: The size and complexity of the pool play a significant role in determining the shooting time. A smaller pool with a simple design will generally take less time to shoot gunite compared to a larger pool with intricate features such as stairs, benches, or waterfalls. Additionally, irregularly shaped pools or pools with unique designs may require more time and attention to ensure consistent thickness and coverage.
- Crew Skill and Experience: The skill and experience of the crew members involved in shooting gunite can greatly impact the time it takes to complete the process. An experienced and efficient crew that is well-versed in gunite application techniques can work more quickly and effectively, leading to a shorter shooting time. Conversely, a less experienced crew may take longer to complete the process as they need to be more cautious and deliberate in their approach.
- Weather Conditions: Weather conditions can also affect the shooting time for gunite. Ideally, gunite should be shot in dry weather conditions with low humidity and moderate temperatures. Extreme temperatures, high winds, or precipitation can impact the efficiency of the gunite application process. For example, high heat can cause the gunite to set faster, which may require the crew to work at a faster pace. On the other hand, rain or excessive humidity can cause the gunite to cure unevenly or have a weaker bond, which can slow down the shooting process.
- Other Factors: Other factors that can influence the shooting time include the availability of equipment, the access to the pool site, and any interruptions or delays that may occur during the process. It’s important to account for these factors when estimating the shooting time for gunite.
In order to get an accurate estimate of the shooting time for gunite, it is best to consult with a professional pool contractor. They can assess the specific project details, such as the size and complexity of the pool, and provide a more accurate timeline based on their experience and expertise.
Tips for Efficient Gunite Shooting
Efficient gunite shooting is crucial for a smooth and successful pool construction project. It helps save time, reduces costs, and ensures a high-quality pool structure. Here are some tips to consider for efficient gunite shooting:
- Proper Planning and Preparation: Thorough planning and preparation are key to efficient gunite shooting. This involves discussing and finalizing the pool design, confirming the desired thickness and reinforcement requirements, and ensuring all necessary materials and equipment are available. Adequate site preparation, including clearing the area and setting up forms, should be completed beforehand to minimize any delays.
- Maintain a Consistent Workflow: Maintaining a consistent workflow helps to maximize efficiency during gunite shooting. This involves coordinating with the crew members to ensure everyone knows their responsibilities and tasks. The crew should work systematically, moving in a logical and coordinated manner to ensure complete coverage and consistent thickness. Effective communication between crew members and the nozzleman is crucial in maintaining a smooth workflow.
- Optimize Mix Ratios: The mix ratios of the gunite, including the cement, sand, and water proportions, should be optimized for efficient shooting. It is important to strike a balance between achieving proper workability and avoiding excess moisture or slump. An experienced crew can fine-tune the mix ratios to ensure a consistent and workable gunite mixture.
- Minimize Downtime: Minimizing downtime is essential for efficient gunite shooting. This involves ensuring a continuous supply of gunite mixture to the nozzleman, minimizing the need to stop and start the application process. Having designated crew members responsible for the consistent supply of gunite from the hopper to the nozzle helps maintain a steady workflow. Efficient management of equipment, such as compressors and hoses, helps avoid delays due to breakdowns or malfunctions.
- Utilize Proper Nozzle Techniques: The nozzleman plays a crucial role in efficient gunite shooting. Proper nozzle techniques and control are essential for consistent application. The nozzle should be held at the correct angle and distance from the surface to ensure even coverage. The nozzleman should work methodically, moving the nozzle smoothly and steadily to avoid inconsistencies in thickness or coverage. Regular training and practice can help nozzleman develop efficient techniques.
- Optimize Crew Size: The crew size should be optimized for efficient gunite shooting. Having too many crew members can result in overcrowding and confusion, leading to inefficiencies. Conversely, having too few crew members can delay the process and result in inadequate coverage. Identify the optimal number of crew members needed for the size and complexity of the pool and assign responsibilities accordingly.
- Proper Equipment Maintenance: Regular maintenance of the equipment used for gunite shooting is crucial for efficiency. This includes inspecting hoses, compressors, and nozzles and addressing any issues promptly. Routine cleaning of the equipment helps prevent clogs and blockages that can disrupt the gunite application process. Proper care and maintenance of the equipment ensure that it remains in optimal condition, reducing the risk of breakdowns or delays.
- Continuous Training and Skill Development: Regular training and skill development are important for the crew members involved in gunite shooting. Ensuring that they are up-to-date on the latest techniques, equipment, and safety practices helps improve their efficiency and productivity. Cross-training crew members also helps ensure flexibility and provides backup in case of emergencies or absences.
Safety Precautions
Safety precautions are of utmost importance during the process of shooting gunite. This step involves the use of heavy equipment and the application of a high-pressure material, which poses potential risks to both the construction crew and the surrounding environment. By following necessary safety measures, homeowners and pool contractors can ensure a secure and accident-free construction process. Here are some key safety precautions to consider:
- Personal Protective Equipment (PPE): All crew members involved in shooting gunite should wear appropriate personal protective equipment (PPE). This includes safety goggles or glasses to protect the eyes from flying debris or gunite particles. Gloves should be worn to protect hands from abrasions or chemical exposure, and hearing protection should be used to minimize the impact of loud equipment noise. Additionally, respiratory protection, such as respirators or dust masks, should be used to protect against inhalation of gunite dust.
- Training and Certification: It is important that crew members involved in shooting gunite have received proper training and certification in operating the equipment and following safety protocols. This includes training on handling gunite machines, understanding the appropriate mix ratios for the gunite mixture, and proper nozzle techniques. Adequate training ensures that the crew members have the necessary skills to safely and effectively carry out the gunite application process.
- Safe Working Environment: Creating a safe working environment is crucial to prevent accidents and injuries. The pool construction site should be well-maintained and free from hazards such as loose debris, equipment obstructions, or slippery surfaces. It is important to establish clear walkways and designated areas for equipment and materials to minimize tripping hazards. Adequate lighting should be provided to ensure visibility, especially during early morning or late evening work hours.
- Equipment Safety: Regular maintenance and inspection of the equipment used during the gunite application process is essential. This includes checking for any damages or malfunctions, ensuring that safety features are in place, and following manufacturer guidelines for maintenance and operation. Any defective or damaged equipment should be immediately repaired or replaced to avoid potential accidents or breakdowns.
- Communication and Coordination: Effective communication and coordination between the crew members are vital for maintaining a safe working environment. Clear communication about job responsibilities, safety protocols, and any changes or updates should be prioritized. Additionally, establishing clear communication channels with the nozzleman during gunite application allows for better coordination and ensures the safety and accuracy of the process.
- Emergency Preparedness: Having proper emergency protocols in place is essential to handle unforeseen situations. Crew members should be trained in first aid and CPR, and first aid kits should be readily available on-site. Additionally, access to emergency medical services should be established, and contact information for emergency services and medical facilities should be posted prominently.
- Adhering to OSHA Guidelines: The Occupational Safety and Health Administration (OSHA) provides guidelines and regulations to ensure workplace safety. It is important for homeowners and pool contractors to be familiar with OSHA regulations, as they can provide valuable guidance on safety practices and requirements specific to the construction industry. Adhering to OSHA guidelines helps to protect workers and mitigate potential hazards during the gunite shooting process.
By implementing these safety precautions, homeowners and pool contractors can minimize the risk of accidents and injuries during the gunite shooting process. Prioritizing safety allows for a smooth and secure construction process and contributes to the overall success and quality of the gunite pool. It is essential to remain vigilant and reinforce safety practices throughout the construction project to ensure the well-being of all involved parties.
Weather Considerations
Weather considerations play a significant role in the gunite shooting process, as weather conditions can affect the quality and efficiency of the application. While it is ideal to schedule gunite shooting during favorable weather conditions, it is essential to be prepared and take appropriate measures to work around any weather constraints that may arise. Here are some key weather considerations to keep in mind:
- Ideal Weather Conditions for Gunite Application: Gunite shooting is best carried out in dry weather conditions with mild temperatures and low humidity. Dry conditions ensure that the gunite mixture cures properly and adheres well to the pool structure. Moderate temperatures help maintain an optimal working environment, as extreme heat can cause the gunite to set too quickly, while freezing temperatures can affect the curing process. Low humidity helps prevent excessive moisture absorption by the gunite, ensuring consistent strength and quality.
- Challenges Posed by Extreme Temperatures: Extreme temperatures can pose challenges during gunite shooting. High temperatures can cause the gunite mixture to dry out more quickly, affecting its workability and curing time. Measures should be taken to prevent the mixture from drying out, such as adjusting the mix ratio or adjusting the shooting schedule to work during cooler parts of the day. Cold temperatures can slow down the curing process, potentially causing delays in completing the gunite application. Temporary heaters or insulation may be required to maintain suitable curing temperatures.
- Potential Impact of Precipitation: Rainfall or excessive moisture can have a significant impact on gunite shooting. Rainwater can interfere with the bonding and curing process of the gunite, leading to weaker adhesion and potential surface imperfections. It is generally recommended to avoid shooting gunite during rainy conditions. However, if light or intermittent rain occurs, temporary shelters, tarps, or protective coverings can be used to shield the work area and prevent direct contact between the gunite and raindrops. It is important to consult with the pool contractor and follow their recommendations on dealing with rain during the gunite shooting process.
- Working Around Weather Constraints: To work around weather constraints, flexibility and adaptability are key. Continuously monitoring weather forecasts is crucial to plan the gunite shooting process accordingly. Pool contractors should have contingency plans in place and be prepared to adjust the shooting schedule if adverse weather conditions are anticipated. This may involve rescheduling or temporarily pausing the gunite shooting process until more favorable weather conditions arise.
In situations where weather constraints cannot be avoided entirely, proper protection and prevention measures should be taken. Temporary shelters, tarps, or canopies can be set up to shield the work area from rain or direct sunlight. Additional equipment, such as heaters or fans, can also be utilized as necessary to control temperature and humidity levels.
It is important to maintain open communication and collaboration between the pool contractor, crew members, and homeowners throughout the gunite shooting process. Regular updates and discussions about weather conditions and potential impacts can help ensure everyone is aware of any adjustments or modifications needed to accommodate weather constraints.
By being proactive and adaptable, homeowners and pool contractors can work together to minimize the impact of adverse weather on the gunite shooting process and achieve a successful and high-quality pool construction project.
Can You Shoot Gunite In The Rain
No, shooting gunite in the rain is generally not recommended. Rain can cause several issues that may compromise the quality and effectiveness of the gunite application. Here are some reasons why shooting gunite in the rain should be avoided:
- Compromised Bonding: Rainwater can interfere with the bonding process between the gunite and the pool structure. The presence of water on the surface can prevent proper adhesion and bonding of the gunite mixture, resulting in a weakened structure.
- Uneven Curing: Rain can disrupt the curing process of the gunite. Excess moisture can dilute the mixture, affecting the curing time and causing uneven or inconsistent curing. This can lead to variations in strength and durability across different areas of the pool structure.
- Surface Imperfections: Rainwater can cause surface imperfections on the gunite, such as pitting or uneven texture. The impact of raindrops on the freshly applied gunite can create indentations or disrupt the smoothness of the surface.
- Increased Shrinkage: Moisture from rain can increase the shrinkage of the gunite as it cures. This can result in cracks or shrinkage voids, compromising the structural integrity of the pool.
- Safety Risks for Crew: Shooting gunite in the rain can also pose safety risks for the crew members involved in the process. Wet surfaces can be slippery, increasing the chance of accidents or falls. Rainwater may also make it more difficult to maintain a safe working environment.
However, if there is light drizzle or intermittent showers during the gunite application process, some precautions can be taken to minimize the impact of rain. This may include using tarps or temporary shelters to cover the work areas and protect the freshly applied gunite from direct rainfall. It is important to consult with the pool contractor and follow their recommendations based on the specific circumstances and local weather conditions.
Ultimately, it is recommended to plan the gunite shooting process for a time when the weather forecast predicts dry conditions. This helps ensure optimal conditions for proper bonding, curing, and overall quality of the gunite pool structure.
Potential Challenges and Solutions
Despite careful planning and execution, challenges may arise during the gunite shooting process. These challenges can impact the quality and efficiency of the pool construction project if not addressed promptly. Here are some common challenges that may occur during gunite shooting and potential solutions to overcome them:
Aiming for Consistent Thickness
Challenge: Achieving consistent thickness during gunite shooting can be challenging, especially in complex pool designs or areas with irregular contours. Inconsistent thickness can compromise the structural integrity and aesthetics of the pool.
Solution: Proper coordination and communication among the crew members are essential. The nozzleman should work closely with other crew members to ensure even application and coverage. Using string lines or markers as guidelines can help maintain a consistent thickness. Regular visual inspections and adjustments throughout the shooting process can help address areas that require additional gunite or thin spots.
Nozzle Clogging
Challenge: Nozzle clogging is a common issue during gunite shooting, particularly when using mixes with a high sand content. Clogs can lead to interruptions, delays, and inconsistencies in the gunite application.
Solution: Preventive measures can minimize the risk of nozzle clogging. Filtering the gunite mixture before it enters the hopper or employing a separate sieve system can help remove any larger debris or particles that can cause clogs. Regularly inspecting and cleaning the nozzle, hoses, and other equipment during breaks or downtime can also help prevent clogging. In case of a clogged nozzle during application, the crew should promptly clear the blockage and ensure uniform application upon resuming.
Adjusting the Mix Ratio
Challenge: Sometimes, adjustments to the mix ratio may be necessary during gunite shooting. Factors such as temperature, humidity, or specific job requirements may warrant changes to the mix consistency.
Solution: The crew should be prepared to make adjustments to the mix ratio as needed. This requires close monitoring of the gunite mixture during the shooting process. Adjustments can be made by adding small amounts of cement, sand, or water to the hopper while maintaining the desired consistency. It is crucial to follow the recommended mix ratios and consult with the pool engineer or experienced professionals to ensure proper adjustments for optimal results.
Proper Nozzle Technique
Challenge: Achieving proper nozzle technique is vital for consistent and even application of gunite. Inexperienced or improperly trained nozzle operators may struggle with controlling the angle, velocity, or position of the nozzle, resulting in uneven thickness or overspray.
Solution: Proper training and practice for the nozzle operators are essential to develop effective technique. Regular training sessions can help improve their skills in controlling the gunite spray, maintaining consistent thickness, and avoiding excessive overspray or gaps. Maintaining open communication and feedback among the crew members can also help address any issues and provide guidance to the nozzle operator during the gunite shooting process.
Embark on a journey of gunite pool creation with our expert guides. From initial blueprints to the final touches, these in-depth resources will be your go-to companions for bringing your pool vision to life.
Step by Step Guide to Building a Gunite Pool: Step-by-step guide to constructing your own gunite pool, covering the planning, excavation, construction, and finishing processes to help you create a stunning and durable pool.
How Long Does It Take to Build a Gunite Swimming Pool: Understand the estimated timeline for building a gunite pool, including factors that may affect the duration, and get ready for your dream pool in no time.
Should Gunite Pools Be Built in Cold Weather: Learn about the feasibility of constructing gunite pools during colder seasons and the necessary precautions to ensure a successful build despite the weather conditions.
How to Properly Water a Gunite Pool’s Shell: Get valuable insights on how to water your gunite pool correctly during and after construction, aiding the curing process and maintaining its structural integrity.
How Do You Waterproof a Gunite Swimming Pool: Ensure your gunite pool remains leak-free and resilient by exploring effective methods and products for waterproofing, protecting it from water-related issues.
Conclusion
The process of shooting gunite, also known as dry-mix shotcrete, requires careful planning, skilled labor, and efficient equipment. While the actual time it takes to shoot gunite can vary depending on several factors, such as the size and complexity of the project, the expertise of the crew, and the equipment used, it generally involves a relatively quick application process.
Gunite is pneumatically sprayed onto surfaces, creating a strong and durable layer. The shooting process typically involves a team of experienced workers operating specialized machinery, such as a concrete pump and spray nozzle. These tools allow for precise control and efficient application, reducing the overall time required.
For smaller projects, the shooting process may be completed within a few hours. However, larger and more intricate projects may take several days or even weeks to finish. Factors such as the surface area to be covered, the thickness of the gunite layer, and the need for additional detailing can all influence the duration of the shooting process.
It is crucial to note that while the application of gunite may be relatively fast, the overall timeline of a construction or renovation project involving gunite will be influenced by other factors, such as surface preparation, curing time, and subsequent finishing work. Proper planning and coordination with the construction team are essential to ensure that the gunite application fits into the project schedule effectively.
Ultimately, shooting gunite is a specialized process that requires expertise and attention to detail. By following best practices and utilizing advanced equipment, contractors can ensure a smooth and efficient application, saving both time and resources. Whether used in pool construction, slope stabilization, or other structural applications, gunite proves to be a versatile and durable material, contributing to the longevity and strength of the finished project.
Frequently Asked Questions
1. What is gunite spray?
Gunite spray, also known as shotcrete or sprayed concrete, is a construction technique where concrete or mortar is conveyed through a hose and pneumatically projected at high velocity onto a surface using a spray gun or nozzle. The process involves the forceful projection of the mix, which allows it to adhere firmly and harden to maximum density on the targeted surface. Gunite spray can be applied in both wet-mix and dry-mix forms, with wet mix referred to as shotcrete and dry mix commonly known as gunite.
2. Do you have to spray gunite?
Yes, gunite is typically applied through the process of spraying. Gunite, also known as shotcrete, is a mixture of cement, sand, and water that is pneumatically sprayed onto surfaces using a spray gun or nozzle. The high pressure at which the mixture is sprayed allows it to adhere to the host surface, consolidate, and compact effectively. The spraying technique provides several advantages, including efficient and rapid application, reduced labor requirements, and the ability to shape and reinforce complex structures.
3. How do you spray gunite?
Spraying gunite involves using an air compressor to mix dry cement and sand particles with water, then using a hose and nozzle to spray the mixture onto a surface. The sprayer should be held at a consistent distance from the surface in order to ensure even coverage. After spraying, it is important to use additional tools such as hand trowels or steel-toothed rakes to finish shaping the gunite and remove any excess material. Once finished, the gunite should be allowed to cure for 24 hours before use.
4. How long does gunite take to cure?
The curing time for gunite, which refers to the hardening and gaining of strength of the cement and sand mixture, can vary depending on several factors such as weather conditions, humidity, and the size of the pool or structure. Typically, the curing process for gunite pools takes between 28 to 30 days. During this time, it is important to take special care of the pool, avoid heavy usage, and maintain balanced water chemistry to ensure proper curing and long-lasting results. To know more, read our how much time does it take for gunite to cure.